Top Five Problems You Can Solve Using Ving
Target Use Cases, Safety Training, and More
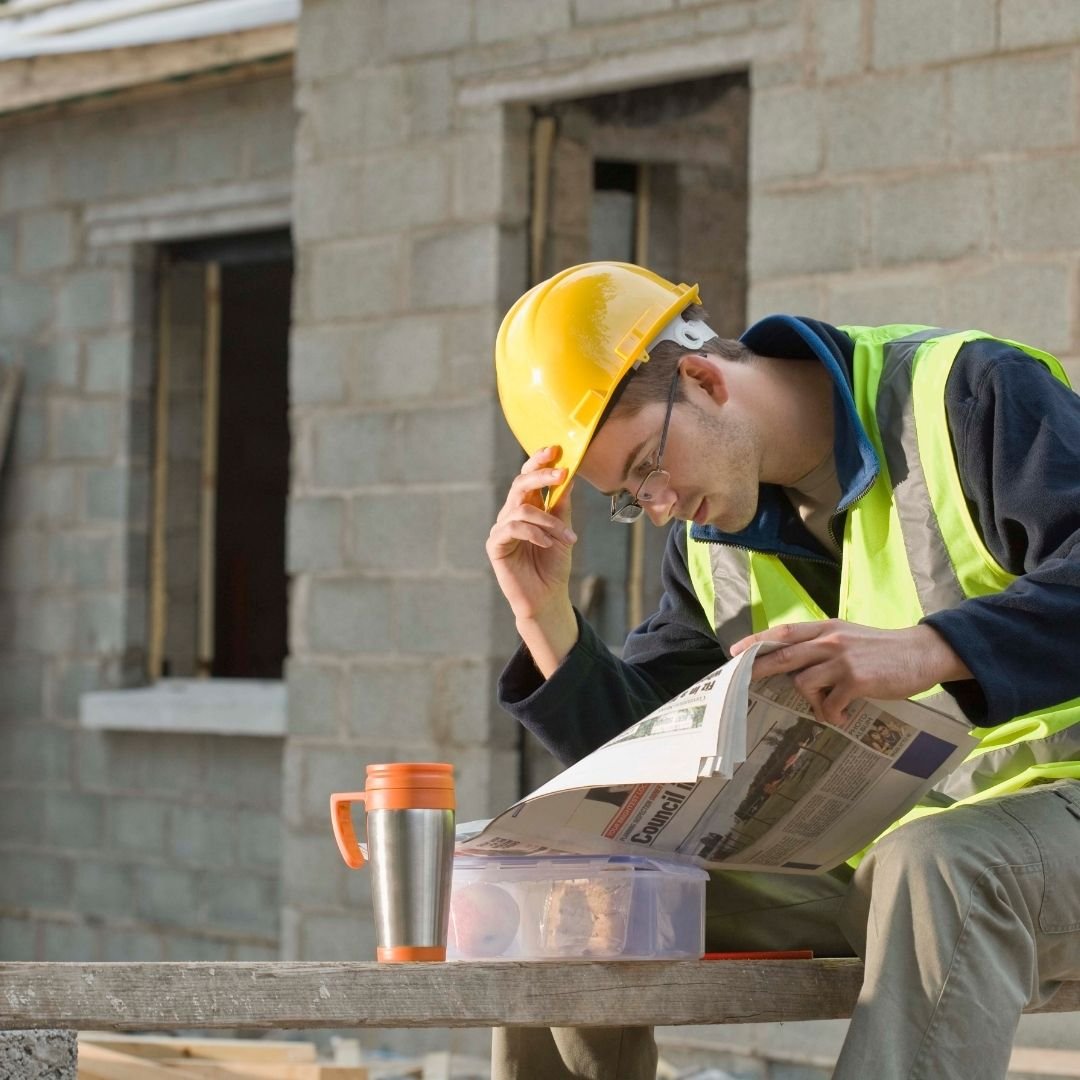
.webp?width=250&height=250&name=Older%20Worker%20Skills%20Transfer%20to%20Younger%20Worker-1%20(1).webp)
#1 Overcome new hire and trade skill development challenges.
Here's the problem nearly all of our customers face. The skilled trades workforce is aging, and younger employees have the highest turnover risk. On average, the turnover rate in the construction/trades industry hovers around 21.4%, with employees 24 or younger reaching about 64%*.
Compounding the statistics above even further, there aren't enough skilled trade workers to fill the number of currently open positions; company leadership has an expensive challenge. Traditional new hire and skills development processes must be revised, shortened, and streamlined to accelerate skills development, empowering on-the-job access and closing the skills gap.
Ving technology enables users to capture the know-how of their subject matter experts and create reusable training assets. Their custom training courses greatly accelerate skill development and drive new hire/existing employee productivity. Customers own the training they make and have access to the asset long after their SME is no longer available.
*DHI Group's Hiring Indicators report
-1.webp?width=300&height=300&name=3-3-1%20(1)-1.webp)
#2 Increase employee engagement with critical on-the-job information.
Gone are the days of plopping someone in a chair for a live lecture or watching a 30-minute video. Today's employees (modern learners) require a different approach. Learners need to feel empowered and have real-time access to job-related information.
Fact: the average attention span is decreasing. While videos are one of the most engaging mediums, on average, they can only keep the attention span of an individual for 2.7 Minutes.
Imagine your conference room - employees watching a video or listening to someone speak. You not only have to pay for the speaker/video, pull everyone off the job, pay for their time during, to, and from training, food, etc. Are you getting your money's worth?
Hermann Ebbinghaus Theory (not rocket science, but very accurate) states that humans start losing the memory of learned knowledge over time, in days or weeks, unless the learned knowledge is consciously reviewed time and again.
Did you know?
-
Within one hour, people will have forgotten an average of 50%
-
Within 24 hours, they have forgotten an average of 70%
-
Within a week, they have forgotten on average of 90%.
Ving Safety Program users leverage the power of Microburst Training to drive trainee engagement with course content, promoting retention, recall, and re-use of critical on-the-job information.
Microburst packets consist of high-impact videos, images, infographics, and scored assessments designed to be done in under five minutes.
Users schedule the release of microbursts to keep critical on-the-job information top of mind all the time, reducing the odds of forgetfulness and striving to create habits vs. a one-and-done mentality.
*Hermann Ebbinghaus Encylopedia Britannica
**Digital Information World
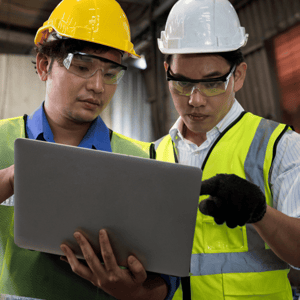
#3 Provide employees with training at a location, on-demand, and for the task at hand.
Are new employees more likely to be injured? According to the Bureau of Labor Statistics, new workers are 5X more likely to be injured on the job than their more experienced counterparts. 40% of all injuries involve people who have been on the job for less than one year, and one in eight injuries happen on an employee's first day. All are very costly scenarios that deserve proactive risk mitigation.
Recurring awareness around the most basic of injuries should be a top priority.
(source OSHA) Per Instance
Injury Type |
Direct Cost |
Indirect Cost |
Total Cost |
Laceration |
$21,872 |
$24,059 |
$45,931 |
Fracture |
$54,856 |
$60,341 |
$115,197 |
Heat Prostration |
$37,658 |
$41,423 |
$79,081 |
Electric Shock |
$158,218 |
$174,039 |
$332,257 |
Ving users ensure their employees have the correct, on-demand information when they need it most. Ving technology generates QR codes that users place near problem areas. Employees become familiar with the Ving QR code as a reminder to stop, think, and review. As needed, scanning the QR code retrieves a "how to get the job done right without injury tutorial.
Requiring new hires to scan QR codes until necessary skills and track records of safe operation is proven reduces the probability and cost related to the injury.
Did any of these use cases hit home? Get you thinking?
Schedule a Discovery Call!
Let us know how to connect with you; get started with the Ving Safety Program today.
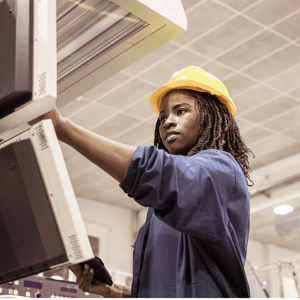
#4 Reallocate valuable employee time from lower-level tasks to higher-level value add.
Over the past five years, we've surveyed over a thousand business Owners and Safety Managers. We discovered that most weekly spend hours on very low-level tasks required to sustain a safety program:
-
Searching for training content on the web
-
Chasing down employees / Finding the time to do the training
-
Aggregating training results
-
Organizing training data into reports
-
Organizing/preparing for training
-
Flying/Driving from site to site
Add in the time they spend delivering training, repeating training for new hires and absentees, and you start to see that the current process demands a lot of time from some of your most valuable, skilled resources. The hard dollars (average salary range of the person accountable is between $65K and $92K per year) and underutilized resource skills add up quickly.
Ving Safety Program users have found that they streamline their administrative efforts and find an optimal balance between in-person and online training that saves weekly hours and expense. Ving enables them to sustain their program more effectively and efficiently. With newfound time in their week, they focus on higher-value add tasks related to the safety program and other critical areas of responsibility.
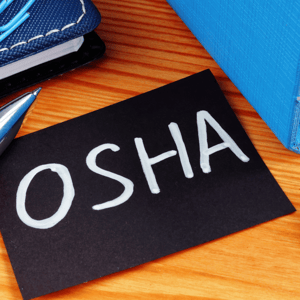
#5 Compliance verification for regulatory agencies and customers.
Non-compliance comes with severe consequences - from personal injury to financial penalties. Sustaining a business process that ensures training compliance with regulatory agencies and customer contracts requires a lot of planning and employee involvement.
All it takes is for one employee to fall through the crack, the one who hasn't finished the training, or worse yet, not even started it, to be asked by OSHA or your customer for proof of training.
Organizations that can adequately demonstrate to OSHA that they have a proactive approach to preventing incidents and eliminating the possibility of a recurring incident have the potential to avoid costly fines.
In addition to OSHA concerns, customer requirements can present a tracking and verification challenge. Customers often require on-the-spot verification of training or scheduled reports to be sent to them verifying each employee completes specific training before entering job sites.
Ving Safety Program users:
-
Access automated, real-time compliance dashboards, providing visibility across their labor force.
-
Having the ability to track employee compliance to any standard, i.e., OSHA, Customer, Job, Task, Geographic, gives them the "heads up" they need to take proactive action before it is too late.
-
Easy access to proof of training is easily accessible by supervisors and individual employees from anywhere in the field via their mobile devices.
Talk To A Ving Expert